Horizontal baler machines (closed-end & open-end)
Compress cardboard & plastic waste into consistent mill-sized bales
Updated on March 22, 2024 | Authors: Pim Brouwer & Brent Nijssen
A horizontal waste baler is an industrial recycling machine for compressing waste materials into dense mill-sized bales. A horizontal baler is cost-effective when your company produces a minimum of 2,000 kg / 4,400 lbs of cardboard or plastic waste per day.
What is a horizontal baler? With a horizontal baler, you compress large amounts of recyclable materials (such as cardboard or plastic waste) into a far more compact shape for easier storage and shipment. There are two types of horizontal balers, a closed-end baler and an open-end baler. The closed-end baler is meant for lower bale production, while the open-end baler is geared towards high production. Lastly, the open-end baler is available in a single-ram and a more powerful two-ram variant.
Find the right baler for your business
Advice and information for horizontal balers
We believe that good advice is very important. Every month we help hundreds of businesses worldwide find the right recycling machine.
- Find the right horizontal baler for your needs
- Our global network of experts are ready to help
- Trusted brands that offer great service and maintenance
Request Expert Advice
Get free advice from trusted experts
Horizontal baler types:
Table of contents
- Horizontal baler types
- Closed-end horizontal baler
- Open-end horizontal baler
- Cost of a horizontal baler
- For who is a horizontal baler?
- Specification explanation
- Prevent jamming with a shear blade
- Tools and equipment
Closed-end horizontal baler
A closed-end horizontal baler is an ‘entry-level’ recycling baler. This baler type is recognized by the closed-off pressing chamber. It is also a smaller baler in comparison to an open-end auto-tie baler.
The waste material is compressed horizontally by a single ram that forces the waste inside a baling chamber against a closed door. Hence the machine is also known as a ‘closed-door baler’. The process of compressing waste is automatic, so there is no need for an operator during baling.
To feed the hopper with cardboard or plastic waste, you can use an optional conveyor. But you can also use a bin lifter, forklift with self-dumping hopper, or feed it manually by hand.
Find the right baler for your business
Advice and information for horizontal balers
On average, a closed-end baler generates 3-5 bales per hour and thus is recommended for processing and compacting low volumes of cardboard or plastic waste.
After the baling process has been completed, the bale needs to be manually tied off by the operator. The rear or side door can be opened when finished, so the pressure is released inside the chamber. The bale is then pushed out by extending the ram or by the next bale that is in production. This type of baler can be used for single-bale output.
Compact horizontal baler
A compact horizontal baling press is the right solution for compacting cardboard waste into bales when space is limited but waste volumes are high. These balers are perfect for retail, supermarkets, and manufacturing industries. On this page, you’ll find a quick overview of space-saving horizontal balers and compactors.
Read more about compact horizontal balers.

Pros of a closed-end baler
- Budget-friendly single ram baler
- Uniform, dense mill-sized bales
- Takes up less space than an open-end baler
- Multiple types of feed openings and configurations
- When baling, new waste material can be fed into the feed opening
Cons of a closed-end baler
- Manual tie-off system
- Produce one bale at a time
- Not a fully automatic baling system
- Baling process takes longer than an auto tie baler
- Requires more space than a vertical cardboard baler
Open-end horizontal baler
An open-end horizontal baler is a ‘high-end’ recycling baler. This automatic horizontal baler machine is characterized by the open rear end of the extrusion chamber and the auto-tie function for the bales.
The open-end type baler is a heavy-duty extrusion baler that compresses high volumes of voluminous waste materials, such as corrugated cardboard. The base variant of the baler comes with an energy-efficient single ram.
But you can also opt for a more powerful two-ram extrusion baler. This type is recommended for higher volumes of (more bulky) waste and is capable of compressing more types of waste streams over a single-ram extrusion baler.
The end section of the extrusion chamber is under constant tension because of the top cylinder. This cylinder performs continuous pressure on the sides of the chamber, which ensures tight and dense bales. For a more smooth output, the cylinder can also loosen up in between the baling process.
Find the right baler for your business
Advice and information for horizontal balers
Open-end balers can continuously bale waste materials. Because of its open end and auto tie system, bales are produced fully automatically.
The main advantage of an auto-tie baler is that the process of baling and wiring the bale is fully automatic, which reduces labor costs. To further optimize and automize the baling process, we recommend making use of a conveyor to feed the baler automatically with waste. Finished dense bales are auto-wired by the baler and only need to be collected and stored manually by a forklift or (electronic) pallet truck.
Pros of an open-end baler
- Flexible, customizable and versatile
- Fully-automatic baling solution
- Bale large amounts of waste materials
- Efficient in use and reduce labor costs
- Hands-off baling operation, for higher safety
Cons of an open-end baler
- High investment costs
- First produced bale is looser
- Not meant for single bale production
- Requires more floor space than a closed-door baler
- Bale lengths can differ and are less consistent
Cost of a horizontal baler
The cost of a horizontal baler machine can get divided into the machine’s cost and the operating and maintenance costs.
The machine itself can be bought in one go, leased, or rented for a specific period. Leasing or renting a horizontal baler spreads out the substantial investment. Still, because the leasing and renting prices can differ per situation, we only focus on the overall cost of the machine.
We split the horizontal balers into a low-volume closed-end group and a high-volume open-end one to give a more accurate indication.
The price of a closed-end horizontal baler:
- New closed-end baler between: $20,000 – $100,000
- Used or refurbished closed-end baler from $15,000
The price of an open-end horizontal baler:
- New open-end baler between: $100,000 – $750,000
- Used or refurbished closed-end baler from $40,000
Check more information about the operating costs of a horizontal baler
Check more information about the difference between a single-ram and dual-ram baler
Find the right baler for your business
Advice and information for horizontal balers
- Find the right horizontal baler for your needs
- Our global network of experts are ready to help
- Trusted brands that offer great service and maintenance
Request Expert Advice
Get free advice from trusted experts
For who is a horizontal baler?
An organization that produces high quantities (more than 20 tons a/month) of recyclable waste streams will gain cost-efficiency and environmental benefits when using a horizontal baler machine. But each industry and warehouse site has different requirements a horizontal baler should meet.
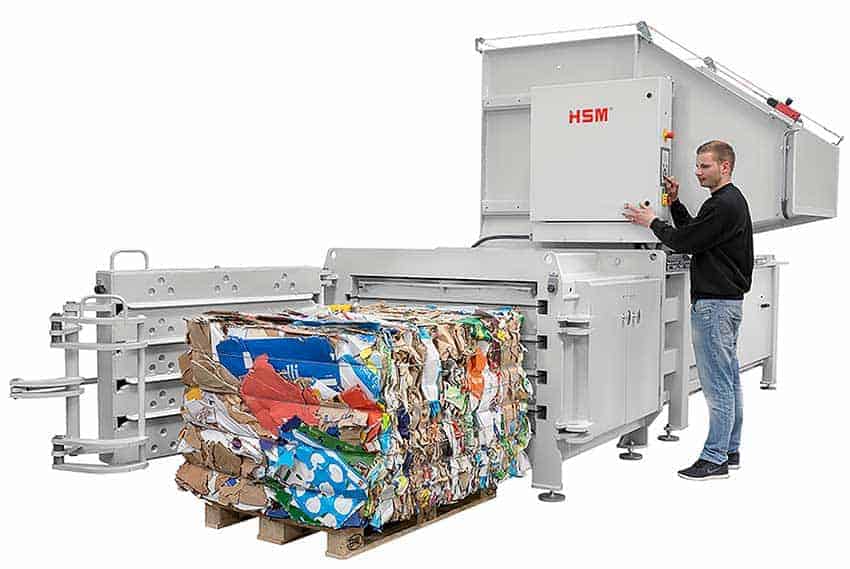
That’s why balers come in a wide array of forms and why a lot of additional components can be added to a baler to complement the users’ situation.
Industries that mainly use a horizontal baler are:
- Distribution, fulfillment & warehouse centers
- Large supermarkets
- Mixed and mono-recycling facilities
- Industry and manufacturing
If floor space is a limiting factor for a horizontal baler, then installing more than one vertical baler could provide a better solution. Or take a look at compact horizontal balers that require minimal floor space.

Request a quote to receive advice from our experts on which type of machine and what setup best suits your facilities’ needs.
Types of material that can be baled for recycling are:
- Paper
- Confidentially/ shredded paper
- Cardboard
- Non-ferrous metals
- Plastics
- E-waste
- Tires / Rubber
- Textiles
Specification explanation
When researching horizontal balers, you will find a lot of technical specifications and information about the machines. Below we describe a few of the most important specifications and explain what they tell about the baler.
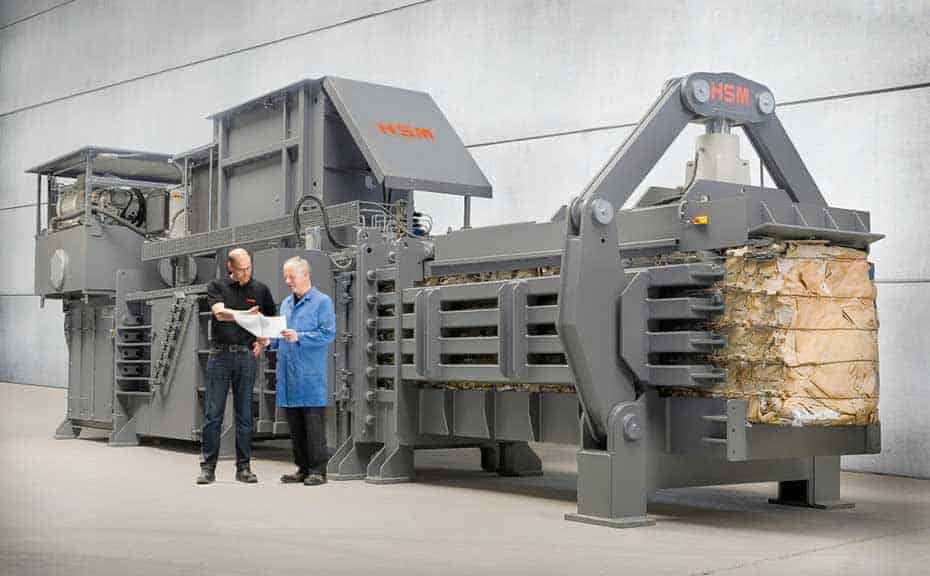
- Motor power: Power of the baler in HP or KW.
- Electrical power: Single or 3-phase power supply.
- Hydraulic pressure: System pressure in PSI or Bar.
- Press force or weight: The number of kilonewton (kN = 102 kg / 224.89 lbs) the ram face can press, also known as ram force or compacting pressure.
- Feed opening: Opening of the loading chute or shaft. A wider feed opening is recommended for large cardboard boxes for instance.
- Production capacity: The output volume (cubic feet or tons) of waste materials the baler can process per hour. The capacity depends on material and input.
- Bale size: The size of a produced bale inside the pressing chamber.
- Expanded bale size: The final size of the output bale outside of the chamber.
- Working cycle time: The time in seconds it takes the baler to perform a standard pressing cycle.
- Oil tank: Capacity (Gallons or liters) of the tank for lubrication.
Prevent jamming with a shear blade
Most horizontal open-end balers have a shear blade installed at the very end of the feed hopper, right before the opening of the baling chamber. The shear blade makes sure that any excess waste material inside the hopper is cut off while the ram compresses the waste inside the baling chamber.
The ram pushes the waste material against the blade, which is then sheared. This shearing action limits the likelihood that the baler gets jammed during the process.
This results in dense bales, but the downside of shearing is that the shear will become blunt over time. It also requires a lot of force to cut through waste materials, such as cardboard. This results in wear on the pressing chamber, as well as on the shearing blade.
Pre-compression lid for no shear baling
A no-shear horizontal open-end baler is a baler without the shear blade. This baler is constructed with a pre-compression lid that allows you to bale without shearing or cutting off the material.
The lid closes off the feed hopper opening and the baling chamber in between the process of feeding waste and compressing waste into a bale. Because the chamber is closed, it also prevents waste materials from being pushed upwards back into the feed chute.
Tools and equipment
Besides the need for the horizontal baler itself, other tools and equipment are required to optimize the process of baling your waste materials. Such as the use of a self-dumping hopper, a recycling conveyor belt, a heavy-duty pallet jack, or a cart tipper for tilting waste containers inside the feed opening of the baler.
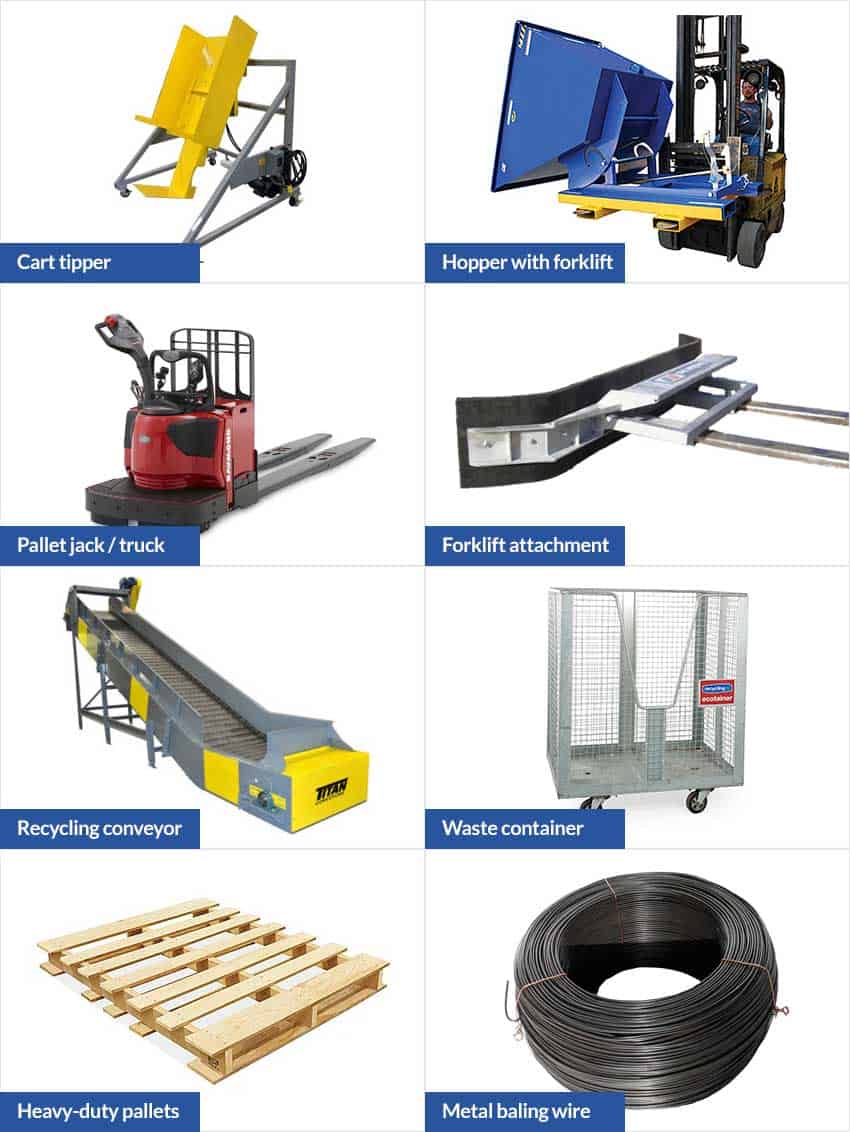
Sources used
- iqsdirectory.com – Types of balers
- crigler.com – Different types of recycling balers
- recyclingtoday.com – Baler guide two ram
- recyclingtoday.com – Baler guide horizontal single-ram balers
- Youtube video #1 – Two Ram Baler Harris TRBT
- Youtube video #2 – Two Ram Baler Olympic Wire and Equipment
By Recycling.com/ 22 February 2023