What are the disadvantages of a vertical cardboard baler?
Things to consider before buying a baler
Updated on Sep. 21, 2021 | Author: Pim Brouwer
A cardboard baler offers many advantages, such as efficiency, improvement of internal logistics, space-saving at your facility, cost reduction, and it also yields higher recycling rates. But there are some disadvantages to be aware of when you consider buying a cardboard baler for your company, as you can read in this post.
Do you want to know more about cardboard baler machines?
14 cons of a cardboard baler:
- High investment
- Necessary tools
- Regular maintenance
- Buy before your try
- Training of employees
- Cardboard waste prices fluctuate
- Use space to save space
- Vertical (indoor) space needed
- Maximum volume
- Not an automated process
- Not all bales are ‘mill standard’
- For cardboard only
- Noise production
- Most balers require 3-phase power supply
High investment
The average cost of a vertical cardboard baler machine sits between $5,000 – $20,000, as we explain in the cost of a baler. The height of the price depends on the specifications you desire and how powerful you want the baler to be. Some manufacturers or resellers offer lease programs for renting a baler. This reduces your initial investment considerably.
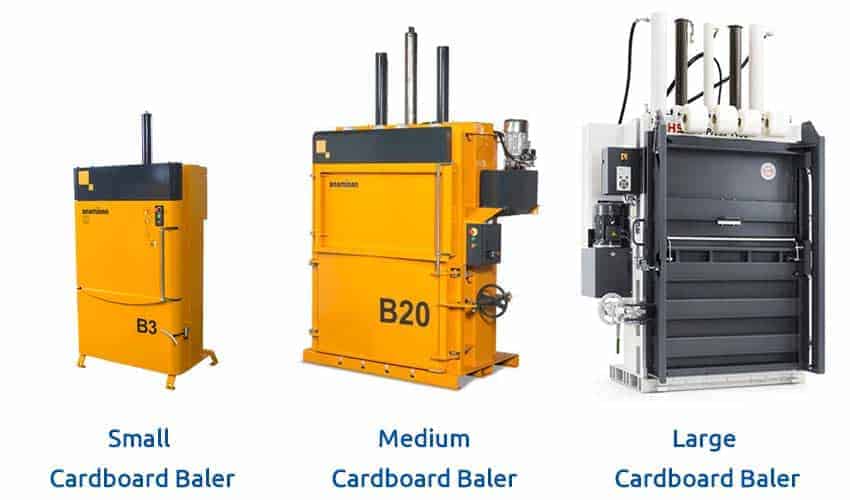
When used effectively and efficiently, a cardboard baler will earn the investment back over time. For example, you reduce the cost of waste hauling and earn revenue by selling your cardboard bales to a mill or recycling company.
Necessary tools
Besides the cost of the machine itself, there are additional costs you should be aware of when you want to use a cardboard baler properly. For instance, you need strapping wire (metal or plastic) that holds the compressed cardboard together into a bale.
These cardboard bales get ejected out of the baler onto a pallet, so you need these pallets as well. You might also need a pallet jack or forklift to transport and lift the cardboard bales at your facility.
Regular maintenance
A cardboard baler is a heavy-duty piece of machinery with moving (hydraulic) parts and electronic components. This means that, in order to run well, a baler needs maintenance regularly. It is recommended to service a cardboard baler every year by a specialist. Most manufacturers offer service contracts for regular maintenance on-site, so you are assured of a well-maintained baler.
When you choose not to perform regular maintenance on your baler, the chances are that the machine will stop working. And this could result in a logistical problem at your facility because voluminous cardboard waste starts piling up quickly and takes up a lot of space.
Buy before your try
A cardboard baler is a large machine that requires a complete installation at your site. That is why it is not very common to try a cardboard baler by installing a demo unit. In other words, you can only test the machine when you buy or lease the actual baler.
You could, of course, ask the seller if you can take a look at a similar baler at a location from another client. This also yields the advantage of asking questions and gathering experiences from real users of the baler.
But, how the baler actually works for your situation will always be slightly different compared to another company. That is why we strongly recommend you to take your time when buying a cardboard baler. It is crucial to gather expert advice.
At Recycling.com, we can help your business get into contact with experts that can help you find the right baler.
Free Download
Ultimate Vertical Baler Overview Sheet
Receive Infographic Now
Get the PDF in your email »
Training of employees
Compressing cardboard into a bale might sound easy. But as you can see in this video, it requires quite some knowledge on how to do this the right way.
Before using a cardboard baler, you need to follow a training program with the operating employees. The type of training depends on the type of baler. A simple light-duty baler is pretty straightforward to use and only requires basic instructions. But a large baler requires thorough instructions to make sure it is used correctly and safely.
Well-trained employees ensure you make the most out of your investment. These trainings result in high-quality cardboard bales, efficiency in the baling process, and lowers safety risks.
Cardboard waste prices fluctuate
Baling cardboard reduces the cost of waste hauling. Because there is lesser transportation necessary for an equal amount of non-compressed cardboard, cardboard bales that have the right bale size for the recycling industry and contain high-quality cardboard also have value. This means you can sell your cardboard bales, especially when you have lots of cardboard bales. Recycling companies use the material to reuse as source material for new cardboard.
The price of a metric ton of cardboard fluctuated roughly between $20 and $210 in the past five years.
The worth of a cardboard bale depends on multiple factors. Such as the weight of the bale, the type of cardboard, and the quality of the material. But the most important factor that determines the price is the current value of the material at the world market.
This value constantly fluctuates and doesn’t yield a fixed rate income. When there is high demand for cardboard, prices go up and yield more from your cardboard waste. On the other hand, when demand for cardboard is low globally, prices will decrease and could even result in a negative value.
Do you want to know more about cardboard baler machines?
Use space to save space
One of the main arguments to invest in a cardboard baler is reducing the volume of cardboard waste. The waste material is quite voluminous and thus requires space at your facility, space you rather want to use for storing products you sell for instance.
A cardboard baler compresses cardboard and reduces the volume of the material. It can reduce the volume of cardboard by up to 95%, depending on the pressing force of the baler.
This reduces the volume of your waste drastically. But, the machine and also the produced cardboard bales still require floor space. So, make sure you exactly know where you want to install the cardboard baler and where you can store the cardboard bales.
We recommend storing cardboard bales under dry circumstances. Keeping cardboard bales dry prevents the material from decreasing in value. You can stack cardboard bales to save up on floor space. But make sure the bales are stacked properly and safely.
Besides, keep in mind that you need a (wheeled) container to store and transport generated cardboard waste towards the baler temporarily. These containers also require floor space.
Vertical (indoor) space needed
A vertical cardboard baler is meant for indoor use. This means it will be installed inside your facility, and like we’ve already mentioned, this requires floor space. But besides that, you also need to have vertical space since it is a machine with a vertical pressing mechanism.
Tip: What is the size of a cardboard baler?
Vertical balers are taller than horizontal balers and require extra ceiling height. Large cardboard compressors need an average of 12-14 feet of vertical space to work correctly. Standard balers have their pressing cylinders on the outside of the machine and thus require extra height.
You can choose a cardboard baler where the cylinders are all installed inside the machine, but these types of cardboard balers are more expensive.
Maximum volume
A cardboard baler comes in small, medium, and large variants. But also, the extra-large vertical balers do have a maximum amount of bales they can produce per hour. The number of bales that a baler produces per hour depends on the baler. For smaller machines, you can count on 3-4 bales per hour. For the larger ones, it is 1 or 2 per hour because the bales are larger.
When you have lots of cardboard waste, you might need multiple cardboard balers at your site to process all the material. This is the tipping point where you need to decide whether it is more cost- and time-efficient to invest in a horizontal cardboard baler set up, which can handle higher volumes of cardboard waste.
Free Download
Ultimate Vertical Baler Overview Sheet
Receive Infographic Now
Get the PDF in your email »
Not an automated process
Baling cardboard with a vertical baler is not a fully automated process. It still requires manual labor. Firstly the cardboard waste is collected, then the cardboard goes into the chamber, and once full, the machine needs to be operated by a trained employee. When the process is finished, the compressed cardboard needs to be strapped with strapping wire, and this is all a manual process.
Then the bale is ejected on a pallet and needs transportation to the storage area for the material. Lastly, the operator needs to prepare the cardboard baler for the next batch of cardboard waste.
As you can see, a baler demands time from employees, which means it costs money to operate. Like already mentioned, it is important to train employees well on how to use a cardboard baler. This reduces the amount of time an employee needs to use the baler correctly.
Not all bales are ‘mill standard’
When you want to sell your cardboard bales to a recycling company, make sure that the produced bales are the correct size. Especially smaller balers produce cardboard bales that are not ‘mill standard’, which may result in higher costs for transportation and higher processing cost of the material.
Professional recycling companies work with industrial-sized bales that have certain measurements. These measurements are used to make sure that transportation costs are as low as possible. Besides measurements, the recycling company also wants to make sure that the bale has the correct weight. So the compression of the cardboard is very important in order to make sure that the bale contains the most weight of cardboard.
For cardboard only
A cardboard baler is meant for compressing cardboard into a bale. Some balers can also compress plastic foil or textile into a bale. It is important to keep in mind that the machine should be used for pressing one type of waste material only and only use it for waste material that the machine can handle.
When using it for cardboard, make sure only cardboard boxes and other clean cardboard material enter the pressing chamber. Throwing other waste materials into the chamber, such as plastic, wood, or even metal, is not recommended. You are then mixing different types of waste materials into a bale result in a worthless end product. Also, you may even damage your baler because of using it for the wrong kind of material.
Ensure employees are instructed well on how to use a cardboard baler so they don’t misuse the machine or even see the baler as a regular waste container.
Noise production
Vertical balers are machines that are meant for inside use. Before installing the baler in your facility, keep in mind that the machine generates noise when it is in use.
Generally, a cardboard baler generates around 55-70 dB when processing cardboard into a bale. But, the baling process takes some time, which means the amount of noise is constant and might be annoying to employees working in the area of the baler.
Baling cardboard doesn’t make a lot of noise, but you might offer the operator hearing protection. Noise above 70 dB over a prolonged period may start to damage your hearing.
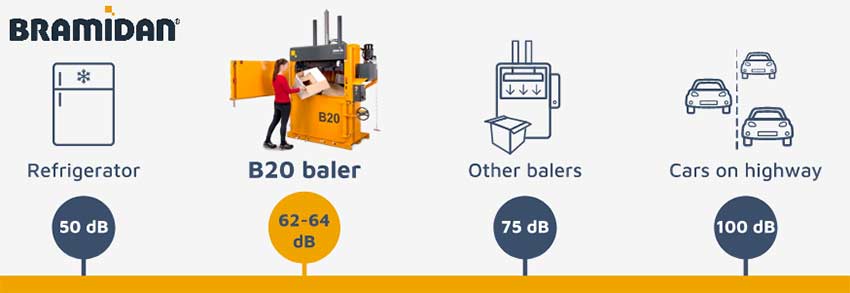
Most balers require 3-phase power supply
Compressing cardboard demands lots of pressing power. The standard single-phase power supply is sufficient for light-duty balers, but when you are more demanding and want to press higher quantities of cardboard into dense bales, it is required to make use of three-phase power. Basically, a three-phase power supply transmits three times as much power as a single-phase. To make use of three-phase power, you need to upgrade your current single-phase service.
The cost of upgrading single-phase service to three-phase service is currently $7 to $10 per linear foot.
In the specifications of the cardboard baler you can find out what power supply is needed. Learn more about the difference between single-phase and three-phase power.
Which baler is right for you?
We believe that the advantages of a cardboard baler outweigh the disadvantages. But it is, of course, useful to know about some of the cons before you invest in a vertical baler.
Choosing the right baler for your needs requires expert advice. And we are here to help you find the best baler for your company. You can read more about vertical cardboard balers here or request a free quotation. We make sure that one of our experts contact you as soon as possible.
The Ultimate Vertical Baler Overview Sheet
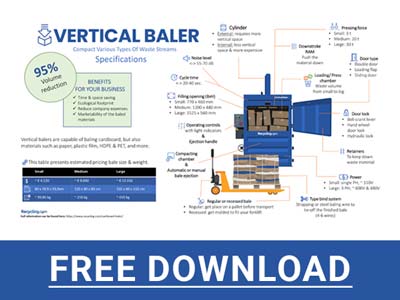
Receive Infographic Now
Get the PDF by email »
Find the right baler for your business
Advice and pricing for cardboard balers
We believe that good advice is essential. Every month we help hundreds of businesses worldwide find the right vertical baler.
- Recycle waste and reduce cost on waste collection
- Our global network of experts are ready to help
- Trusted brands that offer great service and maintenance
Check cardboard balers
Get free advice from our experts
By Recycling.com/ 30 September 2021